What Is Quality Management? A Complete Guide
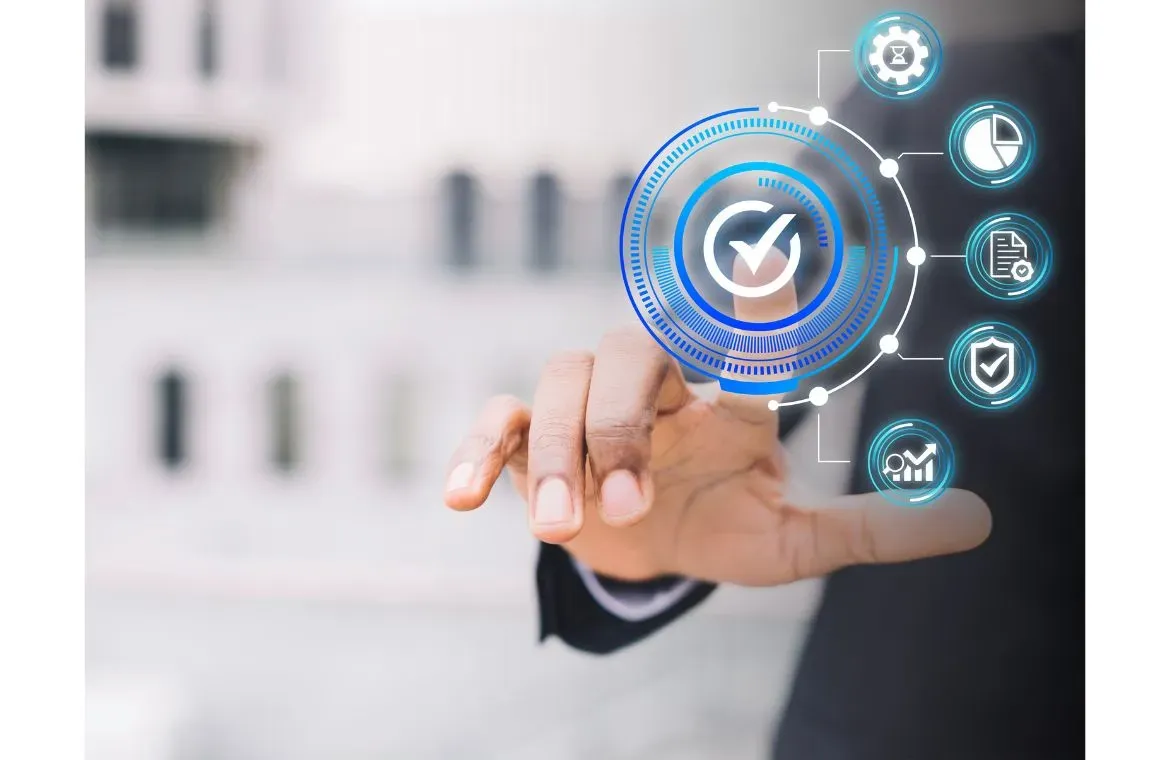
Quality is about how well something performs its intended function, and maintaining quality plays a vital role in leading an organization towards success.
Imagine walking into a restaurant where every dish tastes exactly as good as the last, every interaction feels seamless, and every detail is thoughtfully executed. And you feel like it's the luckiest day of your life because you can never imagine anything like that happening, but let me tell you that’s not just luck, it's how well the quality has been maintained and managed.
From the way a product is designed, to how it's delivered, and even how customer feedback is handled, that’s how quality management holds it all together
Your organization's success now depends on quality management that works in all operations. Companies using quality management see better efficiency, less waste, and happier customers. This article outlines the basics, key parts, and practical applications of quality management to enhance your organization's performance and drive environmentally responsible growth.
What is Quality Management?
Quality management serves as both a view and a way to boost customer satisfaction, cut costs, and remove errors throughout an organization. The core concept revolves around monitoring all activities and tasks necessary to maintain a desired level of excellence.
Why does Quality Management matter in modern organizations?
Quality management creates a framework that helps companies improve continuously and ensures they deliver the best possible products and services. The system helps organizations work together to meet customer and regulatory needs while making operations more effective.
Companies that use quality management see many benefits. They meet customer needs better, which builds trust and brings more sales and repeat business. On top of that, it makes shared compliance with regulations easier while delivering services in a budget-friendly way.
Quality management reduces waste, prevents mistakes, lowers costs, and creates training opportunities. Organizations can work more consistently and utilize their time and resources more effectively.
Principles of Quality Management
Quality management rests on seven core principles that lead organizations to excellence. This framework helps achieve consistent quality and drives organizational success.
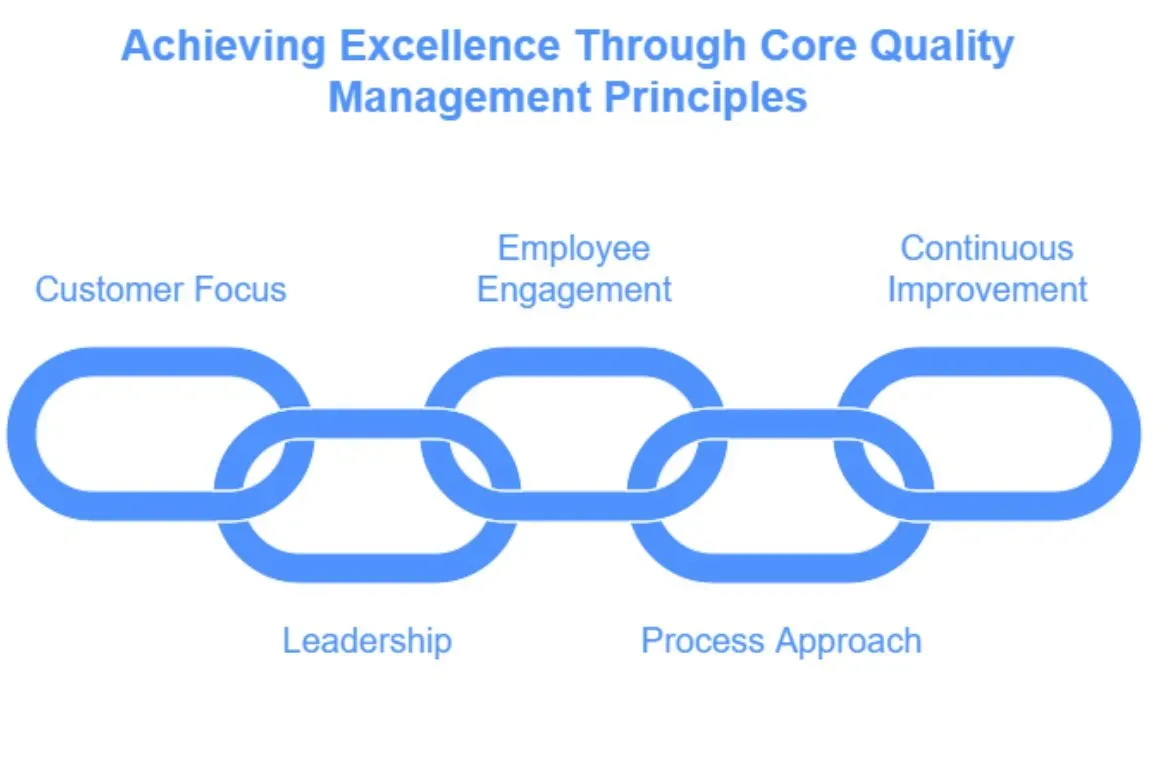
Customer focus and value delivery
Quality management's core lies in meeting and surpassing customer expectations. Companies that put customers first see better value creation, higher satisfaction rates, and bigger market shares.
Success comes from connecting business goals to customer needs. Organizations must spread these needs across teams and build lasting relationships with their customers.
Leadership and cultural alignment
Strong leadership creates clear purpose and direction. Leaders who demonstrate quality commitment see it permeate the entire organization. This shapes culture and motivates staff.
Quality management systems need leaders who own the process. They must clearly state quality policies and goals while creating space to welcome employee ideas.
Employee engagement and accountability
People make an organization work at every level. Staff who participate in quality management better understand its goals. This builds their dedication to quality culture and helps them grow professionally.
Companies should help teams see their work. The goal is to equip them to take quality initiatives confidently and recognize their quality contributions
Process approach and operational consistency
Results come faster when teams manage activities as connected processes in one system. Organizations can examine operations as distinct processes to optimize and improve over time.
Setting up process-based quality management needs detailed process definitions. Teams must identify inputs, outputs, and who does what.
Continuous improvement as a mindset
Top organizations make continuous improvement their primary goal. They mix small changes with big innovations through Plan-Do-Check-Act cycles.
Teams should check progress against proven standards. This works best when process experts get involved and teams use both preventive and reactive approaches.
Evidence-based decisions and data use
Data-driven decisions lead to better outcomes. Teams need to pick the right data to collect from trusted sources. The right people should see this information when needed.
Smart choices come from mixing hard evidence with hands-on experience. This approach makes operations run more efficiently and shows how processes actually perform.
Relationship management across the value chain
Long-term success depends on solid relationships with suppliers, partners, and customers. Good relationship management weighs quick wins against future benefits.
Partners need shared goals and values to work together smoothly. Organizations must pick key stakeholders, focus on important relationships, and cooperate on growth projects.
Components of Quality Management
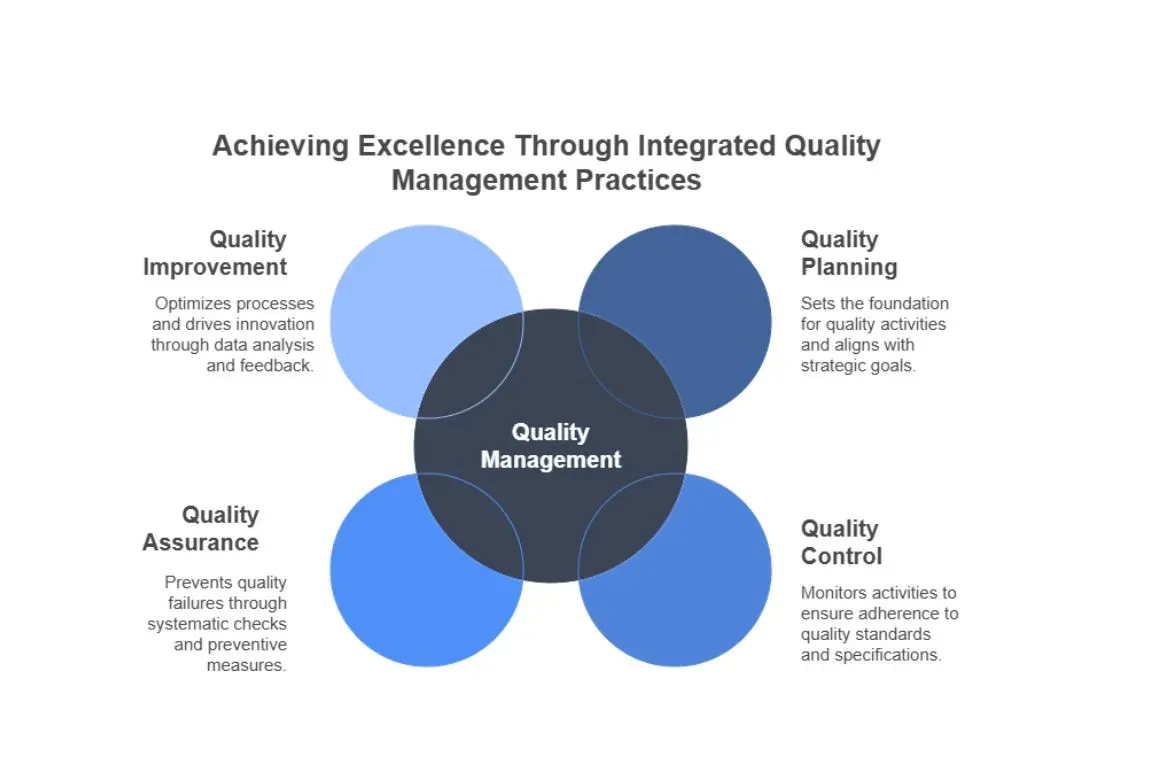
Quality management has four connected parts that work together for organizational excellence. These parts create a systematic cycle. Companies use this cycle to plan, implement, check, and improve the quality of everything they do.
Quality planning and strategic alignment
Quality planning sets the foundation for all quality activities. It designs processes that meet set goals under normal conditions. Organizations should connect quality planning with their overall strategic plans.
Quality planning helps determine project priorities during the planning stage. This ensures everything follows specifications. A complete quality plan lists objectives, process steps, responsibilities, and documented standards.
Quality control and performance monitoring
Quality control reviews are conducted when teams need to take corrective action. Teams monitor specific activities to follow quality standards. This reactive component looks for defects in products or services after they have been developed. Quality assurance prevents issues from happening. Quality control checks if products meet specifications through physical testing.
Quality assurance and risk mitigation
Quality assurance prevents quality failures before they occur. This systematic process checks if products or services meet requirements. It builds customer confidence and company credibility.
Quality assurance activities include process audits, training, documentation reviews, and system implementations. Good QA identifies possible quality issues and creates solutions before they affect deliverables. These preventive steps help organizations create defect-free products that customers expect.
Quality improvement and innovation cycles
Quality improvement finds better ways to work by optimizing processes, products, and services. Teams identify areas for improvement, make changes, and track results through data analysis and feedback.
Organizations often use methods like Six Sigma, which employs a define, measure, analyze, improve, and control (DMAIC) approach. Some use the Plan-Do-Study-Act (PDSA) cycle for quick improvements. Both methods link process changes to outcomes. This helps organizations create lasting quality improvements that drive innovation.
Benefits of Quality Management in an Organization
Quality management brings clear benefits that show up in many areas of business performance. Companies that use quality management become more competitive and better respond to what the market wants. They also do better financially, both now and down the road.
Improved customer satisfaction and loyalty
Quality management makes customers happier by delivering products and services that meet or beat what they expect. Studies show that organizations with quality management systems create increased customer value. They also see better satisfaction scores and stronger loyalty, which leads to more sales and repeat business.
Operational efficiency and cost reduction
The money saved through quality management adds up quickly. Quality management cuts operating costs in several ways. It identifies and removes inefficient processes, prevents mistakes before they occur, reduces rework, and automates routine tasks.
Stronger brand reputation and market trust
Quality management builds the foundation for a strong brand reputation in today's competitive market. Your organization earns credibility and trust from customers and partners by consistently meeting quality standards. It also protects a reputation through risk management, which identifies and resolves potential problems before customers become aware of them.
Examples of Quality Management in Different Industries
Quality management practices vary across different industries. Each sector adapts core principles to meet its specific challenges and needs. A close look at these adaptations gives an explanation of successful implementation strategies.
- Manufacturing: Lean and Six Sigma integration: Manufacturing excellence typically combines Lean methodology with Six Sigma techniques. This combination helps companies spot process weaknesses, track performance improvements, and create standardized operations. Companies that use quality management systems see better supply chain visibility, fewer product failures, and faster breakthrough cycles.
- Healthcare: Patient safety and compliance: Healthcare quality management focuses on ensuring patient safety while meeting regulatory requirements. Modern healthcare systems recognize that errors come from system failures rather than individual mistakes. This understanding shifts improvement efforts toward better processes and structures.
- Technology: Agile QA and DevOps: Tech sectors welcome DevOps and Agile methods that transform quality assurance from a final check into a core development component. DevOps QA testing combines quality practices throughout development with continuous testing and automation. QA experts add strategic value when they design automated test cases, select the right tools and frameworks, and move testing earlier in the development process.
- Retail: Customer experience and feedback loops: Retail quality management prioritizes the customer experience. Good feedback systems turn customer comments into ongoing conversations, rather than static data. Many retailers use loyalty programs as a foundation to improve quality. These programs provide customer details and buying histories that help create customized experiences.
Conclusion
Quality management is the lifeblood of organizational excellence. It reshapes how businesses deliver value to customers and optimizes operations. Organizations achieve remarkable improvements in customer satisfaction, operational efficiency, and market position.
Leadership commitment and active participation from all levels drive successful quality management. Your organization's quality improvement experience begins when you understand customer needs, establish clear processes, and create a culture of continuous improvement.
So, your next steps should include assessing current quality practices and identifying areas for improvement. Business management courses can prove to be a great choice for gaining the right expertise and building a comprehensive quality management system that aligns with your organization's goals and industry requirements.
Your organization will achieve lasting success through better customer satisfaction, lower operational costs, and a stronger brand reputation. Quality management goes beyond procedures. It's a strategic approach that changes how you deliver value to customers and builds lasting competitive advantages.
Frequently Asked Questions
Q1. What are the key principles of quality management?
Quality management is based on seven core principles: customer focus, leadership, people engagement, process approach, continuous improvement, evidence-based decision making, and relationship management. These principles guide organizations in delivering consistent quality and driving success.
Q2. What do you mean by quality management?
Quality management is a systematic approach to ensuring that products, services, and processes consistently meet or exceed customer expectations and organizational standards. It involves planning, controlling, assuring, and improving quality across all areas of a business.
Q3. What are the main components of quality management?
The four main components of quality management are quality planning, quality control, quality assurance, and quality improvement. These components work together in a cycle to ensure organizations plan, implement, verify, and improve quality across all operations.
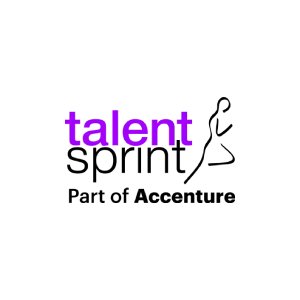
TalentSprint
TalentSprint is a leading deep-tech education company. It partners with esteemed academic institutions and global corporations to offer advanced learning programs in deep-tech, management, and emerging technologies. Known for its high-impact programs co-created with think tanks and experts, TalentSprint blends academic expertise with practical industry experience.