Digital Manufacturing and Smart Factories: Shaping the Future of Production
Digital Manufacturing and Smart Factories
Last Updated:
September 24, 2024
Published On:
November 29, 2024
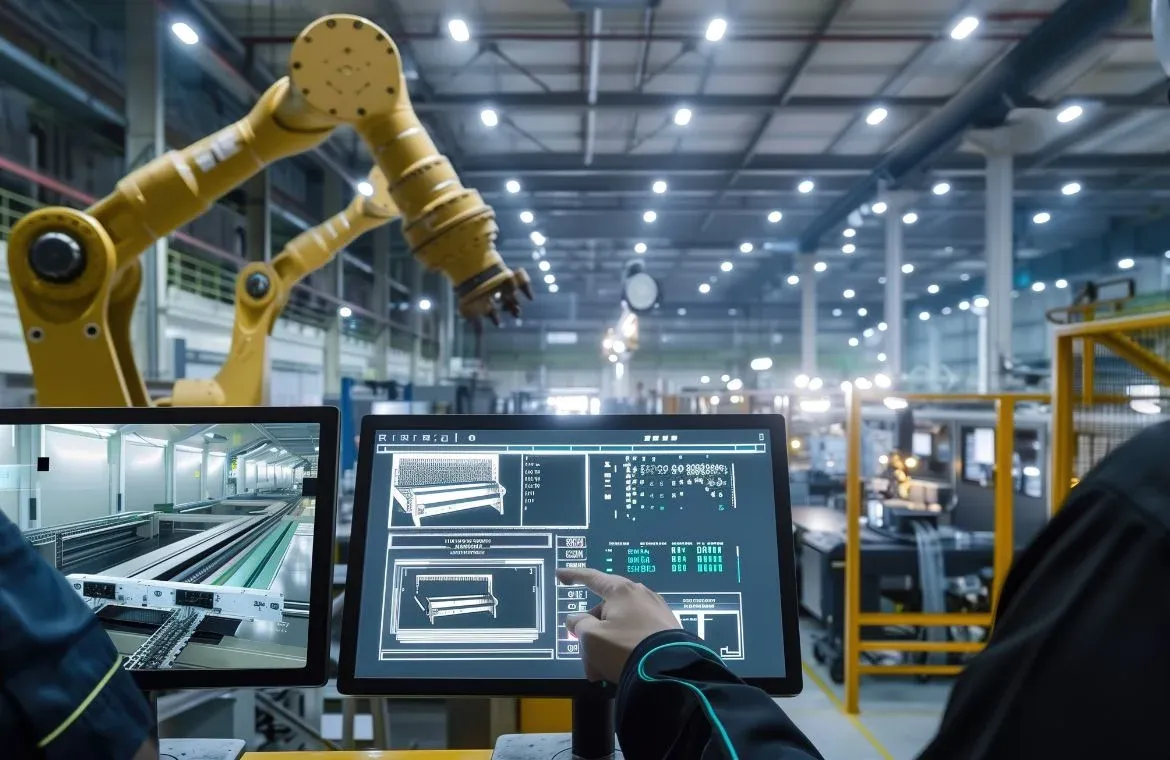
If we look back on how the world was four years ago when that global pandemic hit the whole world, the entire world went into hibernation physically. It was during that time that we realised the absolute value of the internet. It took us on a journey from the real world to the virtual world of innovation and advancement; only then did we realise how the world was evolving, from industries to education, from information to entertainment. The manufacturing industry also went to heinous growth, thanks to digital manufacturing and smart factories, which combined automation and state-of-the-art technology to build production systems that are easier to adapt, intelligent, and efficient in doing their work.
The digital transformation journey of digital twins and smart factories exemplifies this digital mindset and points to a future in which digital technology will propel aerospace innovation.
“Advanced trainer aircraft, the T-7A Red Hawk, is a trailblazing example of digital pathfinder technology in aviation.”
Imagine a factory where minimum human participation is required for machines, robots, and even artificial intelligence (AI) to operate together seamlessly, making choices in real time, increasing quality, and decreasing waste. That’s how digital manufacturing and smart factories work together.
Introducing the World of Digital Manufacturing
“The power of digital manufacturing lies in its ability to transform ideas into concepts and those concepts into innovative goods.”
Digital manufacturing is an integrated approach to manufacturing that uses computer technologies to enhance production processes. As the number of automated tools in manufacturing facilities rises, businesses must implement digital systems to track, evaluate, and simulate every machine to maximise efficiency. Design, integration, adaptability, efficiency (or "lean-ness"), and design are the objectives of digital manufacturing.
By 2025, the digital manufacturing sector is predicted to have grown to $767.82 billion. Among other nations, India considers manufacturing to be essential to the nation's digital transformation plan.
Why Build Expertise in Digital Manufacturing?
The world is evolving on a very fast rate, and Manufacturers continue to invest in digital transformation projects in an effort to tackle industry difficulties such as workforce shortages and growing competition, as well as to adapt to the ever-changing market conditions. To accelerate the conversion to digital production, the most innovative businesses are putting information systems and sets combining technological remedies into place.
Gaining the right expertise can help you grow personally and professionally:
Growth in the career
Digital manufacturing experts are in great demand, which makes high-paying positions available in sectors like consumer goods, luxury commodities, aerospace, and automotive. Having this knowledge improves one's professional possibilities and enables one to spearhead creative endeavours.
Innovation Leadership
Digital manufacturing experts play an important role in fostering innovation by spearheading the use of technologies such as 3D printing, AI, and the Internet of Things, which are revolutionising production processes and enabling customised solutions.
Advanced problem solving
Experts in digital manufacturing are better suited to handle difficult problems because they can use cutting-edge analytics and real-time data to enhance operational efficiency and product design.
Knowledge of digital manufacturing enables progress in one's work, spurs creativity, and helps create more sustainable, effective production methods.
Here are the few examples of how digital manufacturing is actually reaching heights
- Digital manufacturing is becoming a reality as a result of the increased digitization brought about by the quick uptake of cutting-edge technologies like AI, IoT, etc. Manufacturing is becoming more dynamic and intelligent.
- The market for digital manufacturing is predicted to develop quickly, from $263 billion in 2019 to $767 billion by 2025. Digitising their production value chain is already a priority for almost two-thirds of industrial enterprises globally.
- As the industrial sector embraces this digital revolution, experts with deep tech knowledge and an understanding of the manufacturing ecosystem are now needed to spearhead the transition.
The Smart factory of the future
A smart factory means a highly digitalized and robotic production environment where systems, devices, and workflows are connected via technologies such as data analytics, artificial intelligence (AI), and the Internet of Things (IoT).
The entire manufacturing process is made adaptable, useful, as well as responsive to fluctuations that occur in these facilities by using real-time data for monitoring, optimising, and improving production efficiency.
Over the last several years, business executives have realised how critical digital transformation is to supply chains and manufacturing operations if they are to remain resilient and competitive in the 2020s.
The pandemic also revealed loopholes in the worldwide supply chain and in the business.
“According to a Forbes magazine piece that reaffirmed this, the industrial business should already be aware of what COVID-19 has shown the world. Modern production ecosystems and supply chains are ineffective, so we must switch to a more flexible, agile approach that is entirely digitally empowered”.
How Digital Manufacturing and Smart Factories are Changing Production
Through the integration of technologies like IoT, AI, and augmented reality across the entire manufacturing process, digital manufacturing and smart factories are revolutionising production by enabling real-time data analysis, increased automation, and flexible customization. This results in improved efficiency, higher product quality, faster production times, and the ability to quickly adapt to changing market demands.
What Specialised Role in Digital Manufacturing Professionals Can Explore?
An integrated approach to manufacturing is known as "digital manufacturing", and there are many types of digital manufacturing that one can explore, such as:
Product life cycle
Buying, manufacturing, customer service management, and engineering design come next in the product life cycle. Data analytics can take into consideration modifications and oversights that can affect the full life cycle at every stage.
Value chain management
The goal of value chain management is to keep inventories small, combine methods, and satisfy customer requests by minimising resources while continuously evaluating value at every stage of the chain., etc.
Let’s take into consideration some real-world examples of the potential of Digital Manufacturing:
Big Data and Analytics Tools
The industrial value chain can be broken down into actionable information for demand forecasting with the use of data analytics techniques like artificial intelligence and machine learning. To maintain operational efficiency and lower energy usage, for instance, a car factory employs these supply-network management tools to visualise the flow of manufactured parts and raw materials across the network.
Advanced Robotics
In factory settings, robotics is a common sight, automating monotonous jobs to increase productivity and safeguard workers. However, as robot technology advances, more complex activities can be automated. Examples from today's world include automated arms that a person may control in a three-dimensional space in order to replicate certain motions.
Professionally, Digital Manufacturing has a broader scope in today’s fast-growing world,
- Digital manufacturing manager: A person with the ability to create and carry out a comprehensive multi-year manufacturing strategy and plan is a digital manufacturing manager or specialist.
- AI or machine learning engineer: AI, or machine learning, engineers program robotics and produce predictive analytics to help with production.
- Supply chain analyst: Analysts use data to estimate and plan for demand, reducing mistakes, increasing productivity, and spending less money and time.
Individuals' personal and professional growth can be greatly benefited by taking an advanced course in digital manufacturing. From a professional standpoint, it gives them modern facilities and abilities in fields like automation, IoT, AI, and additive manufacturing. It allows them to take on highly specialised roles in industries with great need. Acquiring proficiency in these technologies enables people to spearhead creativity, enhance productivity, and promote sustainability, rendering them invaluable resources for their establishments. Possibilities for leadership, career progression, and higher-paying jobs become available with this expertise.
The PG Level Advanced Certification Programme in Digital Manufacturing and Smart Factories will promote flexibility, problem-solving skills, and ongoing learning, enabling students to take on challenging tasks and stay ahead in a field that is changing quickly. It also gives them more confidence when utilising new technology.
Summed up
In a nutshell, smart factories and digital manufacturing are genuinely changing the face of production. Imagine working in a workplace where humans and robots work together seamlessly, as demonstrated by the autonomous machinery (cobots) at BMW's Leipzig plant, or where real-time data is used, similar to Siemens' digital twin technology, to identify maintenance needs before a breakdown happens. These developments involve more than simply flashy new technology; they also involve more intelligent, effective, and responsive production procedures. Businesses may simplify operations and provide the foundation for a more flexible and sustainable manufacturing future by adopting these advances. Being a part of this change at an exciting moment is worthwhile, as each improvement and modification moves us closer to an industrial world that is more intelligent and productive.
Also, there’s a probability that by 2025, the digital manufacturing sector will witness growth of $767.82 billion. As smart factories reinvent manufacturing occupations, there will also be an increased demand for tech-savvy experts who can further guide the industry's digital transition.
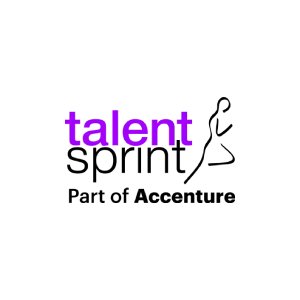
TalentSprint
TalentSprint is a leading deep-tech education company. It partners with esteemed academic institutions and global corporations to offer advanced learning programs in deep-tech, management, and emerging technologies. Known for its high-impact programs co-created with think tanks and experts, TalentSprint blends academic expertise with practical industry experience.