What Is a Smart Factory? A Beginner’s Guide
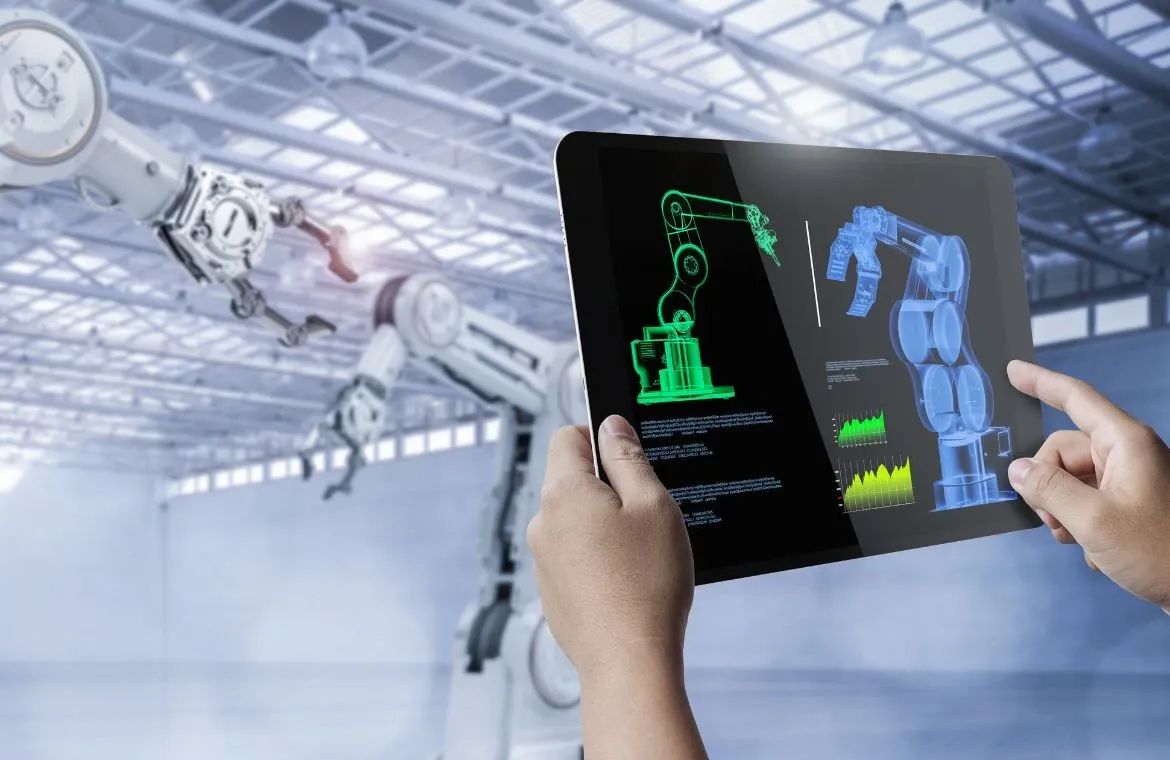
Imagine a factory where machines communicate with each other, production lines resolve their issues, and every nut and bolt knows exactly where it needs to be.
That’s the world of Smart Factories.
This article will dive deeper into what makes a factory "smart," the technologies behind this transformation, and how these state-of-the-art solutions help overcome common manufacturing challenges. Smart factories are essential to stay competitive in Industry 4.0 - whether you work in automotive, aerospace, pharmaceuticals, or energy sectors.
What is a Smart Factory?
A smart factory is a fully digital manufacturing facility that uses connected systems, machinery, and innovative technology to create and analyse data non-stop. Initially introduced as part of Industry 4.0, smart factories connect the physical and digital worlds to create a production environment that's more responsive, quick, and adaptable.
Smart factories work as cyber-physical systems that use innovative technology to analyse data, run automated processes, and learn from experience. This manufacturing system collects and shares data through connected devices, machinery, and production systems. The data helps make better decisions and solve problems.
Also Read: Digital Manufacturing and Smart Factories: Shaping the Future of Production
Why Smart Factories matter today?
India is at the cusp of a major industrial transformation. With its booming economy, ambitious Make in India initiative, and a growing emphasis on digital infrastructure, the need for smarter, more efficient, and resilient manufacturing systems has never been more urgent.
Consumer expectations drive the development of smart factory technologies. The "Amazon Effect" demonstrates how consumer demand for next-day delivery continues to rise, prompting manufacturers to match this speed and efficiency.
How Do Smart Factories Work?
Smart factories build on connected systems that gather, analyse, and use data. These advanced manufacturing spaces work like self-improving ecosystems. Machines and systems talk to each other to make production better without humans watching all the time.
1. Data collection through IoT sensors
The Industrial Internet of Things (IIoT) acts as the smart factory's nervous system. Connected sensors and devices collect data from every part of production. These sensors track temperature, vibration, pressure, and electrical current throughout manufacturing. Simple items like production line bins now have sensors that ask for refills when supplies get low. This constant data gathering marks the first stage in smart factory progress. Manufacturers now collect huge amounts of information from assets in supply chains and factory floor machinery.
2. Real-time monitoring and control
Data flows to central platforms that process it for quick insights. Supervisors can spot production bottlenecks and use resources better. The collected information helps make decisions based on evidence to improve manufacturing. Up-to-the-minute monitoring systems have shown great results.
3. Predictive maintenance and automation
Smart factories use advanced analytics and machine learning to spot potential equipment failures. These systems look at past equipment data to schedule maintenance before things break. The system watches machine health, finds issues, and fixes problems or tells staff. When the predictive models spot something wrong, they can schedule maintenance right away to avoid disrupting production.
4. Integration with supply chain systems
Supply chain integration connects smart factories to the bigger manufacturing world. Smart factories connect machines horizontally and link systems vertically. This sends data from sensors to enterprise resource planning (ERP) systems.
With resilient ERP systems, smart factories can spot problems, check quality, cut waste, improve processes, and predict market trends. Connected technologies help businesses react faster to supply issues or demand changes.
What Technologies are being Used in Smart Factories?
Smart factories run on several state-of-the-art technologies that work together to change manufacturing operations. These technologies play unique but connected roles to create fully optimised production environments.
Internet of Things (IoT)
IoT serves as the foundation of smart factories. It creates networks of connected devices, sensors, and software that monitor and optimise production processes. Industrial IoT (IIoT) devices gather significant operational data from machinery and equipment. This gives real-time visibility into manufacturing processes. Connected systems collect information about equipment status, production rates, and environmental conditions.
Artificial Intelligence and Machine Learning
AI and ML turn raw manufacturing data into useful insights by spotting patterns, anomalies, and correlations.
AI algorithms can predict equipment failures before they happen, which cuts unplanned downtime and maintenance costs.
ML algorithms make real-time adjustments to improve energy efficiency and adapt production schedules based on demand changes.
Cloud computing and edge computing
Cloud computing provides massive storage and allows real-time data access from anywhere. This promotes better collaboration and decision-making.
Edge computing brings processing power closer to the factory floor for real-time data analysis and quick decisions. This dual approach improves manufacturing by handling time-sensitive tasks locally while using cloud resources for bigger analysis and optimisation.
Digital twins and simulation
Digital twins create virtual copies of physical assets, processes, or entire production systems. These dynamic models simulate results from real-time factory conditions. This allows "what-if" analyses across production scenarios.
Digital twins help optimise layouts, space use, and inventory needs during factory design. They predict production bottlenecks accurately using live data, which works better than traditional spreadsheet modelling.
Robotics and automation
Modern robots do much more than traditional automated systems. Today's robots use advanced sensors with improved dexterity and precision for manufacturing. Collaborative robots (cobots) work with humans to improve safety in welding, chemical mixing, and other tasks.
Main Elements of a Smart Factory
Five key elements form the foundation of a smart factory. These elements work together to create a connected manufacturing ecosystem. They are the building blocks that make digital transformation possible in modern production.
1. Data integration
Smart factories excel by uniting information from different sources into one clear view. Data integration acts as a central hub that naturally connects production machines, IoT devices, and supply chain systems.
2. Advanced analytics
Advanced analytics stands at the core of smart manufacturing. These autonomous or semi-autonomous systems help uncover deeper insights and create useful recommendations. IIoT sensors collect massive amounts of data that these systems analyse to spot patterns, unusual events, and performance trends.
3. Scalable infrastructure
Cloud computing provides reliable infrastructure that lets smart factories grow and adapt. Manufacturers can adjust their computing power, storage, and networking capabilities through cloud platforms as their needs change.
4. User-friendly interfaces
Accessible interfaces connect complex systems with human operators. Smart factories now use dashboards that show technical data in ways people can understand. Business users can find and fix issues without always needing help from IT specialists.
5. EDI modernisation
EDI modernisation is a vital but often overlooked part of smart factories. Modern EDI systems help manufacturers communicate smoothly with their trading partners. They automate many transactions in purchasing, receiving, shipping, and inventory management.
Benefits of Smart Factories
Smart factories deliver remarkable returns in many business areas. Research shows these advanced manufacturing environments bring clear advantages to organisations worldwide.
Increased efficiency and productivity
Smart factories boost productivity through better operations. These improvements directly affect business results. Companies that speed up their market delivery using efficient supply chains grow revenue faster than the industry average.
Cost reduction through automation
Smart factories cut costs by reducing unexpected downtime with predictive maintenance. This approach saves costs and cuts maintenance time . Physical automation remains a top priority - of manufacturing executives. Smart manufacturing systems also save money by cutting energy usage, while keeping production quality high.
Improved product quality
Smart factories detect defects instantly during production with real-time monitoring. Advanced analytics help manufacturers learn about quality issues and fix them quickly. The system's ability to track processes and data helps catch defects early, which reduces costly returns and recalls substantially.
Faster time to market
Companies can design, develop, and launch new products faster with smart manufacturing. These technologies streamline the entire process from concept to production and cut manufacturing lead times.
Enhanced sustainability and compliance
Smart factory systems optimise resources and reduce waste. Manufacturers using these systems cut energy use. The technology helps with regulatory compliance through real-time monitoring, accurate reporting, and workflow optimisation. This approach improves operations and ESG performance while showing the company's dedication to quality, environmentally responsible practises, and ethical manufacturing.
Challenges and How to Overcome Them
Smart factories offer great benefits, but organisations face several big challenges when setting up these advanced manufacturing environments.
- Integration complexity: Manufacturers often struggle to integrate new technologies with their existing industrial systems. Old equipment and outdated infrastructure create compatibility issues that make smart factory adoption harder. Manufacturers can tackle these challenges with software solutions that connect both old and new machines to automate data collection from equipment of all types.
- High initial investment: Money remains a major barrier to smart factory implementation. Organisations need to think about equipment costs plus expenses for infrastructure upgrades, software implementation, and staff training. Manufacturers often find it hard to get stakeholder support without showing clear returns on investment. A step-by-step approach to implementation works well. This lets organisations start with high-impact areas and slowly grow their smart factory capabilities.
- Workforce skill gaps: The manufacturing industry faces a serious talent shortage. Today's manufacturing jobs need both technical expertise and digital skills in data analytics, IoT implementation, and automation. Manufacturers should focus on training existing employees and building partnerships with educational institutions.
- Scalability and future-proofing: Moving beyond pilot projects creates another major hurdle. Organisations should create clear roadmaps for technology adoption, invest in adaptable solutions, and run continuous learning programmes. This approach helps manufacturers build flexible systems that can evolve with new technology.
Conclusion
Smart factories mark a revolutionary step for manufacturing organisations that seek a competitive edge in the Industry 4.0 era.
Your trip toward smart manufacturing could face several obstacles. These include integration complexities, high original costs, workforce skill gaps, and cybersecurity concerns. A phased approach offers the most practical way forward. This allows you to target key areas first while you build internal capabilities and show incremental value to stakeholders.
Upskilling your workforce through targeted learning, such as the IISc Digital Manufacturing and Smart Factories course, can bridge knowledge gaps and equip teams to navigate the transition effectively.
Manufacturing's future belongs without doubt to organisations that successfully blend human expertise with advanced technologies like IoT sensors, artificial intelligence, and digital twins. Smart factories represent more than just a technological upgrade as, they fundamentally reshape how manufacturing works.
So, the question isn't whether to adopt smart factory technologies. It's about how fast and well you can implement them to secure your position in the fast-changing manufacturing world.
Frequently Asked Questions
Q1. What is a smart factory?
A smart factory is a highly digitised manufacturing facility that uses interconnected systems, sensors, and advanced technologies to continuously collect and analyse data. This data-driven approach enables real-time monitoring, automated processes, and continuous improvement of operations.
Q2. What are the key technologies used in smart factories?
Smart factories utilise several key technologies, including Internet of Things (IoT) sensors, artificial intelligence and machine learning, cloud and edge computing, digital twins for simulation, and advanced robotics and automation systems.
Q3. What challenges come while implementing smart factories?
The main challenges in implementing smart factories include integration complexity with existing systems, high initial investment costs, workforce skill gaps, cybersecurity concerns, and difficulties in scaling beyond pilot projects. However, these can be addressed through phased implementation, strategic planning, and continuous learning programmes.
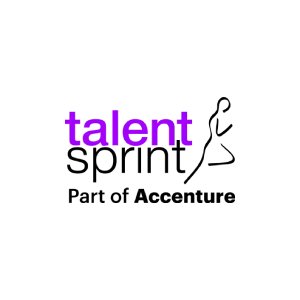
TalentSprint
TalentSprint is a leading deep-tech education company. It partners with esteemed academic institutions and global corporations to offer advanced learning programs in deep-tech, management, and emerging technologies. Known for its high-impact programs co-created with think tanks and experts, TalentSprint blends academic expertise with practical industry experience.